Heavy equipment inspections at makana: +120 points
At makana.com, when we say every machine is backed by a certified inspection, it’s not just a slogan, we mean it. We take heavy equipment inspections seriously because a detailed report gives buyers the confidence they need to make a purchase, clearly showing the exact condition of each machine.
What makes a good machine inspection?
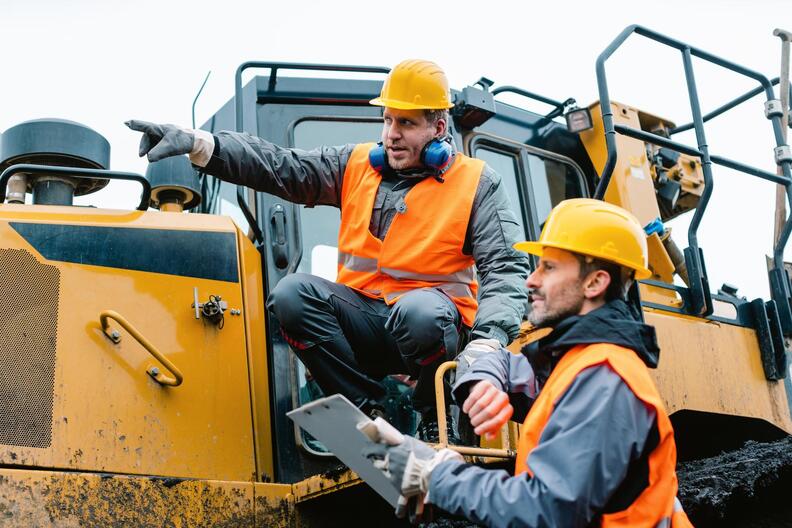
A good machine inspection is comprehensive, covering critical areas like safety systems, engine performance, hydraulics, and undercarriage wear. For example, safety alarms and emergency stop buttons should be tested, not just checked visually.
Hydraulic systems need pressure testing, while undercarriage components like tracks and rollers must be measured for wear. Control stations, including seats and mirrors, are inspected for operator safety and comfort. The best inspections also provide visual proof, such as high-resolution photos or videos, to back up the findings.
In this article, we’ll walk you through our heavy equipment inspection process, using an excavator as an example. We’ll explain the 120 critical points we check to ensure transparency and reliability every step of the way.
The rating system
Before we get into the heavy equipment inspection process, here’s a breakdown of our rating system. Each component is graded on a 1 to 5-star scale:
- Needs attention: Major wear or damage; immediate action required.
- Fair: Functional but worn; maintenance likely needed soon.
- Good: Operating as expected with minor wear; no immediate repairs necessary.
- Very good: Performing well with minimal cosmetic wear.
- Excellent: In like-new condition; no visible wear or issues.
Some inspection points will use an Available/Not Available or Applicable/Not Applicable mark instead of a star rating. This ensures clarity when a standard rating doesn’t apply.
Types of machinery inspection
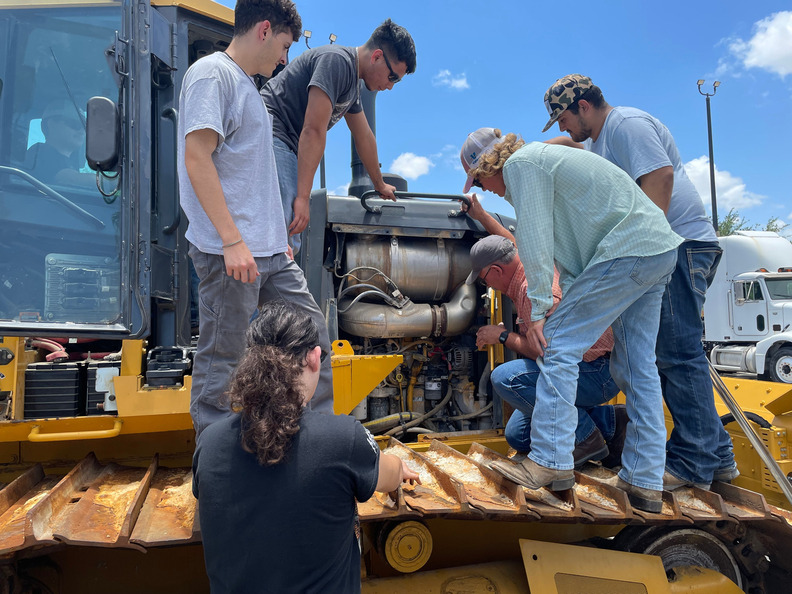
We use three types of inspections during the process: visual, manual, and automated.
- Visual Inspection: A simple walk-around where the inspector checks visible components like plates, glass, and mirrors to ensure they’re intact. There’s no need to operate the machine for this step.
- Manual Inspection: The inspector operates the machine, testing controls and moving parts to assess their condition. This hands-on approach ensures everything works properly under real-world conditions.
- Automated Inspection: Specialized tools are used for precise checks, like measuring track grouser height with a gauge or using diagnostic tools (e.g., an OBDII reader) to retrieve data from the machine’s systems. These tools provide accuracy beyond what visual or manual checks can offer.
Inspection process
For the purpose of this article, we’re looking at excavator inspection, which covers 12 key categories, with a total of 120 detailed checkpoints. The categories include:
General | 11 |
Safety | 7 |
Control station | 9 |
Air conditioner | 5 |
Engine | 22 |
Drive system | 4 |
Hydraulics | 15 |
Electrical | 6 |
Chassis | 5 |
Undercarriage | 16 |
Attachment | 2 |
Oil analysis | 18 |
1. General components inspection (11 points)

This inspection category focuses on key visual and automated checks to ensure the machine’s compliance, condition, and basic functionality. These are the first things our inspectors look at to verify that the machine is up to standard:
- CE Mark (Visual): We check for the CE mark, confirming the machine complies with European regulations.
- Country of Manufacture (Visual): Inspectors verify the nameplate to confirm where the machine was built.
- Emissions Label (Visual): The engine nameplate is checked to ensure the emissions label is present.
- Serial Number (Visual): Inspectors verify the serial number on the nameplate.
- Hour Meter (Automated): We extract engine running hours from the control module and cross-check them with the hour meter.
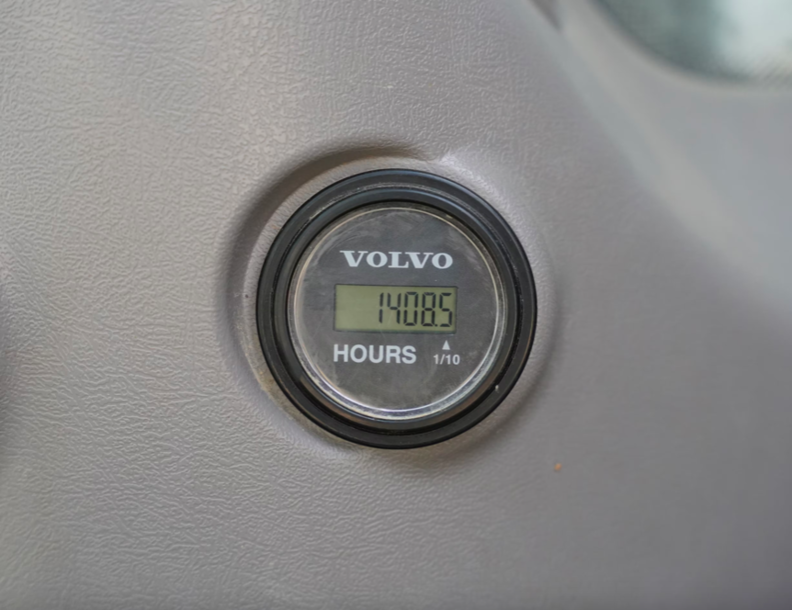
- Fault Codes (Automated): Active and logged fault codes are retrieved from the system to identify any issues.
- Paint (Visual): Inspectors check for cracks, peeling, fading, or discoloration, which may indicate age or poor application.
- Sheet Metal/Fiberglass Condition (Visual): Dents, scratches, rust, or cracks in sheet metal or fiberglass are noted.
- Steps/Ladders (Visual): We check steps and ladders for damage, rust, and structural integrity.
- Handrails (Visual): Rust at joints, cracks, or missing fasteners are inspected to ensure handrails are secure.
- Exterior Lights (Visual): Lights are checked for lens or housing damage and to ensure they’re securely mounted with no loose parts.
2. Safety components inspection (7 points)
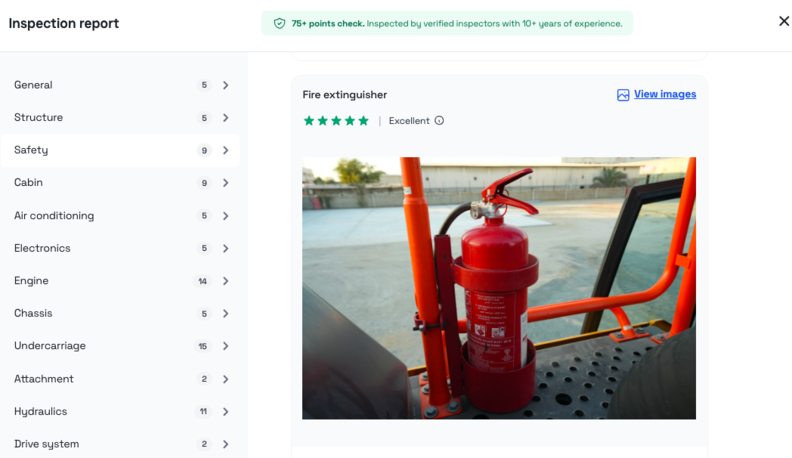
Safety is a top priority in any heavy equipment operation, and our inspection ensures all critical safety components are in working order. Here’s what we check in this category:
- Travel alarm (manual): We test the travel alarm for clarity and volume, ensuring it’s loud enough to be heard over engine noise. It’s activated and deactivated immediately with the travel function.
- Glass (visual): The glass is inspected for cracks, chips, or scratches. We also check the seals for any signs of wear or separation, preventing water leakage, and examine the frame for rust, corrosion, or loose fittings.
- Horn (manual): We verify the horn’s functionality by turning on the machine and pressing the button. The horn should emit a clear, loud sound, any weakness or distortion may indicate an issue.
- Seat belts (visual): We inspect the seat belt for any damage, make sure it retracts smoothly, locks securely, and check that all anchor points and bolts are tightly secured.
- Swing brake (manual): We test the swing brake to ensure it operates smoothly and holds the upper structure without any drifting.
- Hydraulic safety lock (manual): The hydraulic safety lock is checked for damage or wear. We test it by moving the boom and arm through their full range, ensuring smooth engagement and disengagement.
- Safety & operator maintenance manual (visual): We ensure that the safety and operator maintenance manual is available with the machine.
3. Control station inspection (9 points)
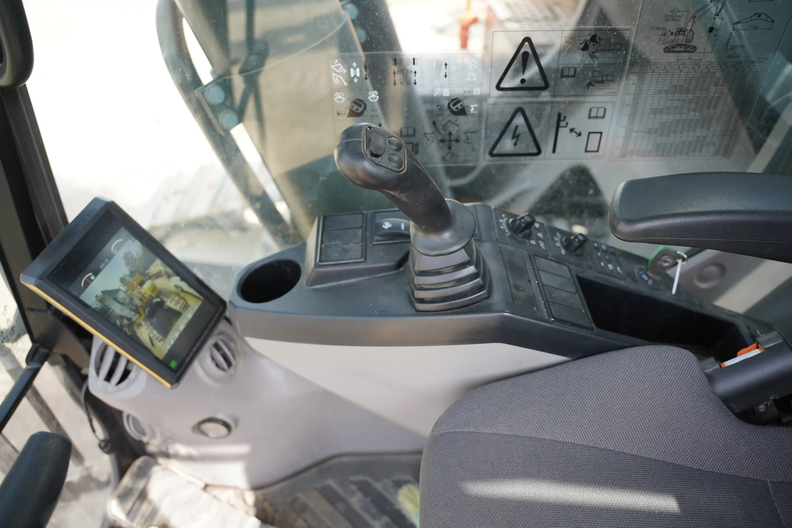
The control station is where the operator spends the majority of their time, so it’s critical that everything is functional and comfortable. Here’s what we check:
- Seats/armrests (visual): We check the upholstery for tears or excessive wear and test seat adjustments, including height, tilt, and lumbar support. Armrests are inspected for smooth operation and secure locking.
- Door handles (manual): Each handle is tested to ensure smooth operation without sticking or resistance. We confirm it returns to its normal position after use.
- Mirrors (visual): Mirrors are inspected for cracks, chips, or scratches that could block visibility. The frame or housing is checked for damage or loose screws.
- Joysticks (manual): Joysticks are checked for damage, ensuring buttons and switches are intact. We test for smooth movement without sticking or jerking.
- Pedals (manual): Pedals are operated through their full range to confirm proper function. We check for wear and damage, focusing on tread patterns and metal components.
- Instrument cluster (manual): Gauges are checked to ensure they’re within normal ranges, and indicator lights are monitored for issues. Switches and buttons on the cluster panel are tested for functionality.
- Electronic instrument board (manual): All control buttons, switches, and knobs are checked for secure attachment and tested for smooth operation and proper function.
- Cabin light (manual): Light covers are inspected for cracks, scratches, or discoloration, ensuring they’re securely mounted. The light is tested to confirm it works properly.
- Radio (manual): We check that the radio display lights up, showing station frequency and audio settings, and verify all radio functions are working correctly.
4. Air conditioner inspection (5 points)
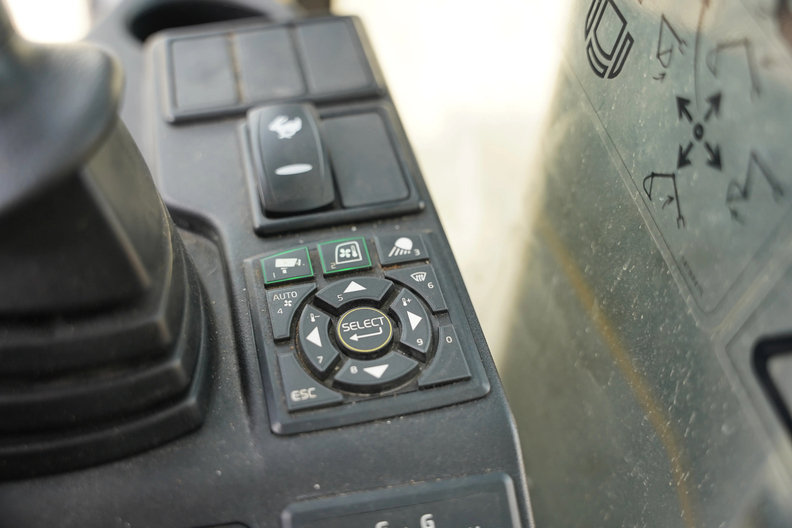
A functional air conditioning system is essential for operator comfort, especially in harsh working conditions. Here’s what we inspect:
- A/C control panel (manual): We check that all controls are securely attached and operate smoothly without sticking.
- Compressor (automated): The compressor clutch is tested for proper engagement and disengagement, and the compressor pressure is verified using a gauge.
- Condenser (visual): We inspect the condenser coils for visible signs of damage, such as bent fins, dents, or corrosion.
- Refrigerant lines (visual): We check for signs of leaks, including oil stains or wet spots around the connections.
- Vents and air flow (visual): Vents are checked for obstructions and cleaned. We also ensure they’re adjustable and properly directing airflow.
5. Engine inspection (22 points)
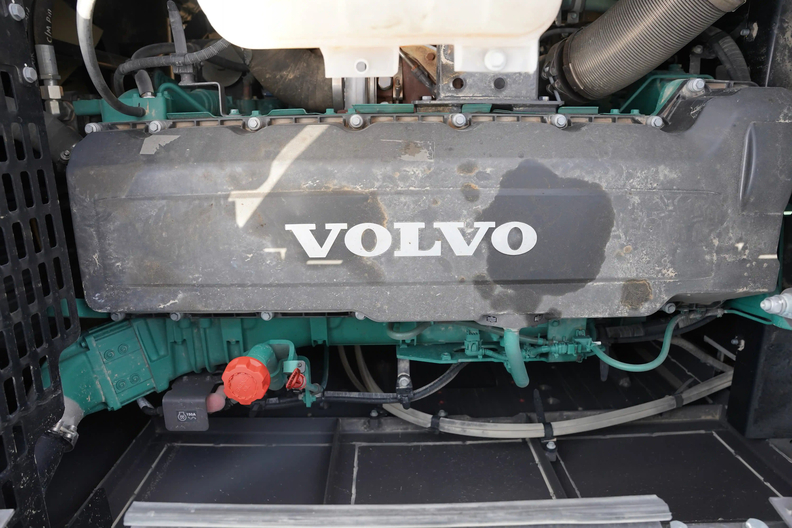
The engine is the heart of the machine, and our inspection ensures it’s performing at peak efficiency. Here’s what we check:
- Engine start check (manual): We listen for any unusual noises during startup, such as grinding, knocking, or excessive vibration.
- Throttle (manual): The engine is started, and the throttle response is tested by gradually adjusting engine speed. We observe engine behavior and listen for any odd noises or vibrations.
- Fuel leakage (visual): We follow the fuel lines from the tank to the engine, checking for any visible signs of fuel leakage.
- Engine oil leakage (visual): Seals and gaskets around the oil pan, valve covers, and oil filter are inspected for any signs of leaks.
- Cooling fan and fan guard (visual): The fan blades are inspected for damage, and the fan guard is checked for obstructions and safety issues, ensuring everything is securely fastened.
- Belts (visual): We check belts for signs of wear, cracking, fraying, or glazing.
- Hoses (visual): Hoses are visually inspected for damage, leaks, and secure connections.
- Engine wiring harness (visual): The wiring harness is inspected for wear, damage, and secure routing.
- Radiator (visual): The radiator fins are checked for any damage, such as bent or crushed fins.
- Oil cooler (visual): We inspect the oil cooler fins for signs of damage, like bent or crushed fins.
- Air cooler (visual): The air cooler fins are also checked for damage, including bent or crushed fins.
- Fuel tank (visual): The exterior of the fuel tank is inspected for damage and leaks, and the fuel cap is checked for proper sealing.
- Engine control module (ECM) (visual): We examine the ECM casing for physical damage, such as cracks, dents, or corrosion, and ensure it’s securely mounted. Connectors and wiring harnesses are checked for any loose, frayed, or damaged wires.
- Engine oil pressure (automated): We measure the engine oil pressure and compare it to the ideal range.
- Fuel system pressure (automated): The fuel system pressure is checked and compared to the expected value.
- Compression test (automated): A compression test is conducted to ensure relevant pressure levels are within normal limits.
- Cylinder cutout test (automated): We use diagnostic tools to perform a cylinder cutout test to isolate any issues.
- Emission control devices (visual): We inspect the AdBlue tank for leaks, cracks, or damage, and ensure the filler cap seals properly.
- Exhaust smoke color (visual): The exhaust smoke is checked for color, which can indicate engine health.
- Turbo (visual): We inspect the turbocharger housing and connections for any signs of damage or leaks.
- Induction system (visual): Intake ducts and hoses are checked for damage and secure installation.
- Exhaust pipe (visual): The exhaust system is inspected for corrosion, rust, or damage. Mounting brackets and clamps are also checked for secure fastening.
6. Drive system inspection (4 points)
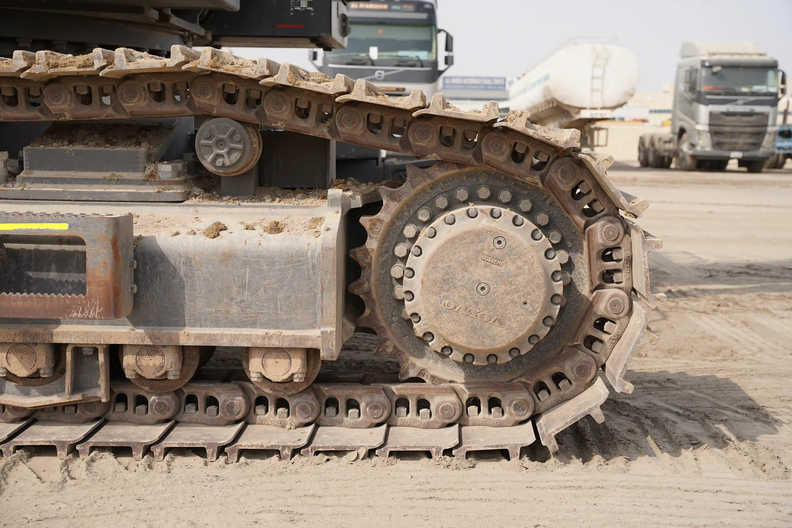
The drive system is essential for the mobility and control of the machine. Here’s what we check:
- Travel function (manual): We operate the travel function in both directions to listen for any unusual noises, feel for vibrations, and ensure smooth movement.
- Travel hours (automated): The diagnostic tool is used to check the total traveled hours.
- Final drive (visual): The final drive housing is inspected for any signs of damage or leaks.
- Travel speed check (manual): We verify the two-speed travel function by rotating each track individually to ensure proper speed and movement.
7. Hydraulics inspection (15 points)
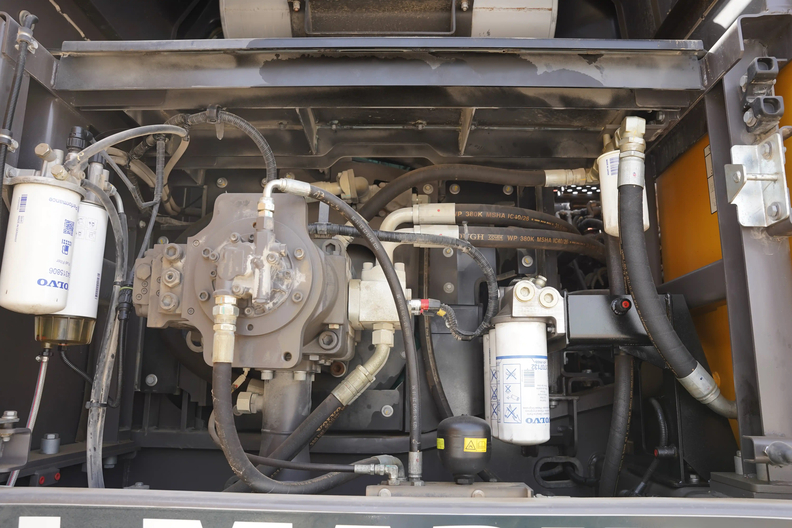
A reliable hydraulic system is key to the performance of heavy machinery. Here’s what we check:
- Hydraulic pump (visual): We check for hydraulic fluid leaks around the pump and inspect for any damage or unusual noises.
- System pressures (automated): Using a diagnostic tool, we measure the hydraulic pump pressures under load to ensure they are within specified limits.
- Hydraulic tank (visual): The hydraulic tank is inspected for signs of damage and leaks.
- Hydraulic hoses and lines (visual): We check hoses, connectors, and fittings for leaks, damage, and ensure all connections are secure.
- Boom lift cylinder(s) (visual): Inspected for cracks, dents, or any impact damage.
- Stick cylinder (visual): Checked for cracks, dents, or signs of impact damage.
- Bucket cylinder (visual): We inspect for any cracks, dents, or damage that could affect performance.
- Hydraulic center swivel (visual): Checked for leaks around the swivel joint and inspected seals and hoses for wear or damage.
- Swing motors (visual): Inspected for leaks and any damage to the motor housing.
- Hydraulic motor (visual): We check the condition of the drive motors and inspect for leaks or damage to the seals.
- Main control valve (visual): Inspected for cracks, rust, corrosion, and oil leaks around the seals. We also check hydraulic lines for wear, cracks, or leaks.
- Hydraulic actuators operation test (manual): The boom, arm, bucket, swing, and travel motors are tested for smooth and consistent operation.
- Attachment piping (visual): We check the piping for any damage or leaks.
- Wiring harness (visual): Inspected for wear, damage, and secure routing.
- Hydraulic pump flow controller (visual): Checked for damage and leaks.
8. Electrical inspection (6 points)
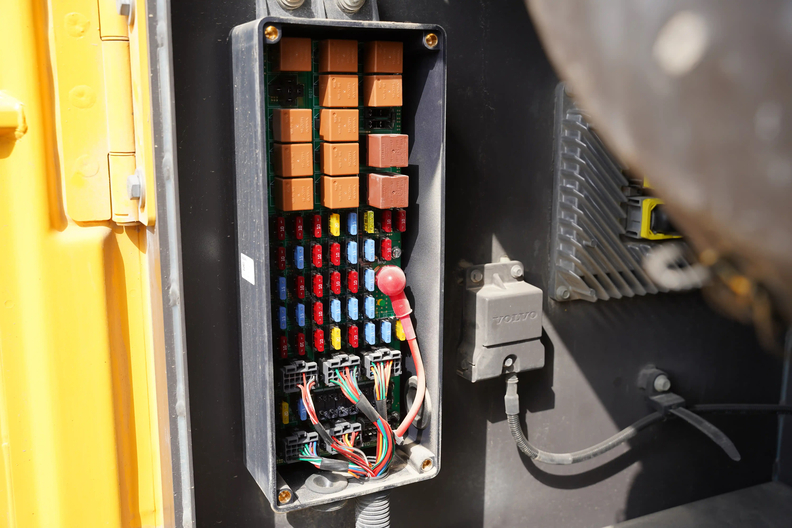
A reliable electrical system ensures the machine operates smoothly and safely. Here’s what we check:
- Main harness (visual): We inspect the wiring harness for signs of wear, damage, and ensure secure routing.
- Battery (visual): The battery terminals are inspected for corrosion, and we check the battery casing and cables for any signs of damage.
- Alternator voltage (automated): Using a diagnostic tool, we record the alternator voltage from live data to ensure it’s within the correct range.
- Lights and signals (manual): All exterior lights and signals are activated and checked for proper function and brightness.
- Fuse box (visual): We inspect the fuse box for any signs of damage, such as cracks, melted plastic, or corrosion.
- Wipers (manual): We activate the wipers to check for smooth operation and listen for any unusual noises.
9. Chassis inspection (5 points)
The chassis components are critical for the machine’s structural integrity and performance. Here’s what we inspect:
- Boom condition (visual): We inspect the boom for visible cracks, dents, or signs of wear.
- Stick condition (visual): The stick is checked for visible cracks, dents, or signs of wear.
- Boom base pin and bushings (visual): Pins, bushings, and pivot points at the boom base are inspected for wear and excessive play.
- Pin and bushings boom to stick (visual): We check the pins, bushings, and pivot points between the boom and stick for wear and excessive play.
- Pin and bushings stick to bucket (visual): The pins, bushings, and pivot points between the stick and bucket are inspected for wear and excessive play.
10. Undercarriage inspection (8 points)

The undercarriage is essential for machine mobility and stability, and we inspect both the left and right sides to ensure durability and performance. Here’s what we check:
- Carrier rollers (visual): We check both left and right carrier rollers for visible cracks or signs of wear.
- Track rollers (visual): Both left and right track rollers are inspected for cracks or wear.
- Track chains (visual): The left and right track chains are checked for visible damage or wear.
- Sprockets (visual): We inspect the left and right sprockets for cracks or signs of wear.
- Idlers (visual): Both left and right idlers are inspected for visible cracks or wear.
- Grouser height (automated): Grouser height is measured on both sides using an ultrasonic tool to ensure it’s within acceptable limits.
- Track tensioners (visual): We check the left and right track tensioners for cracks or signs of wear.
- Track shoes (visual): Both left and right track shoes are inspected for visible cracks or wear.
11. Attachment inspection (2 points)
For attachments like the excavator bucket, we ensure they are in proper working condition. Here’s what we inspect:
- Excavator bucket condition (visual): We inspect the entire exterior surface of the bucket for any cracks, deformities, or damage.
- Excavator bucket teeth condition (visual): The teeth and adapters are checked for wear, and we ensure there are no loose or missing adapters or bolts.
12. Oil Analysis (15 Points)
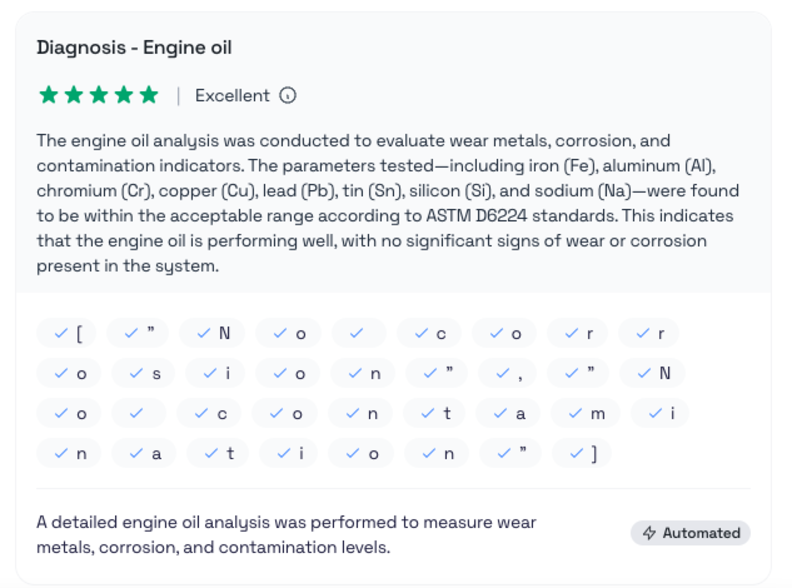
Both the engine and hydraulic oils undergo a detailed analysis to evaluate wear metals, corrosion, and contamination levels. This analysis ensures the internal condition of the machine is sound, offering early detection of any potential issues. The following key parameters are tested according to ISO ASTM D6224 standards.
Wear metals such as iron, aluminum, chromium, copper, lead, and tin are measured to detect component wear. Contamination indicators like silicon and sodium are tested to assess potential contamination from dirt or coolant. Below is a list of the acceptable levels of contamination in engine oil for each element:
- Iron (Fe): Any result below 71 is acceptable.
- Aluminum (Al): Any result below 16 is acceptable.
- Chromium (Cr): Any result below 11 is acceptable.
- Copper (Cu): Any result below 26 is acceptable.
- Lead (Pb): Any result below 26 is acceptable.
- Tin (Sn): Any result below 16 is acceptable.
- Silicon (Si): Any result below 11 is acceptable.
- Sodium (Na): Any result below 16 is acceptable.
As for hydraulic oil, below are the acceptable levels of contamination or wear metals:
- Iron (Fe): Any result below 16 is acceptable.
- Aluminum (Al): Any result below 9 is acceptable.
- Chromium (Cr): Any result below 9 is acceptable.
- Copper (Cu): Any result below 26 is acceptable.
- Lead (Pb): Any result below 11 is acceptable.
- Silicon (Si): Any result below 11 is acceptable.
- Sodium (Na): Any result below 51 is acceptable.
When buying older models of heavy equipment from makana.com, rest assured that our thorough 120-key checkpoint inspection, including checks on working hours, ensures you know exactly what you're getting. This process helps reduce risks and keeps your investment running smoothly! Want to see an actual inspection we’ve done? Head over to our website.